I picked up a German 8.8cm APC projectile with a missing base fuse as part of a complete shell buy, and I've seen the diagrams of these things, and how they are supposed to work. The hardened steel cap below the windscreen has me wondering as one who has worked with alloys of steel all my life and what additives to the steel produce what effective property in a finished steel product. Carbon we all know, but it's mild for hardened steel standards. Adding a little Chrome will do something, Vanadium does something else, Molybdenum does something else too and tungsten and cobalt all impart various performance qualities to a finished steel.
What's got me interested is the metallurgical analysis of not the tungsten carbide type core Germany produced a number of rounds for, but the cheaper and more readily available hardened steel caps that were fitted under the ballistic cap of many projectiles as a substitute for the preferred tungsten cored type.
I read about them, but there was a whole lot of science that had to go into those hardened steel penetrators, and I was just wondering if anybody had ever come across any serious specs on the alloy formula for these types of caps.
Here's some pictures of the thing in question.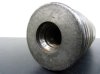
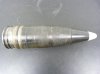
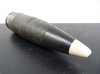
Thanks,
Walt
What's got me interested is the metallurgical analysis of not the tungsten carbide type core Germany produced a number of rounds for, but the cheaper and more readily available hardened steel caps that were fitted under the ballistic cap of many projectiles as a substitute for the preferred tungsten cored type.
I read about them, but there was a whole lot of science that had to go into those hardened steel penetrators, and I was just wondering if anybody had ever come across any serious specs on the alloy formula for these types of caps.
Here's some pictures of the thing in question.
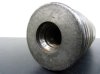
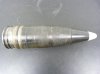
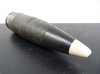
Thanks,
Walt