Stuka
Well-Known Member
Over the years I've bought quite a few projectiles which are missing the original driving bands and I've been searching for options to restore them since. All the options I found weren't really satisfying, so I've always stuck with leaving my projo's as they were, without the bands.
Now I have decided to try something new, something I've been thinking about for a long time: Making real bands, from real copper. It will involve a little bit of surgery for the projo, but it is worth a try. If pictures of projectile-surgery are going to upset you, you might want to turn away for a little while ;-)
This is the patient for today, a 17pr APCBC shell that I bought years ago. The previous owner tried to putty the bands and painted them in copper colour. Looking good from far, but far from good. Step 1 is to remove the putty and measure the width of the missing bands.
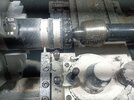
After this I machined the projectile to a smaller diameter.
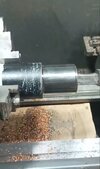
I made a ring from resin to make sand molds and melted scrap pieces of driving band that I saved from previous projects. I casted the molten copper in the sand molds and made two copper rings.
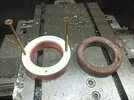
The inner diameter is turned to match the outer diameter of the projectile on the machined part.
I fitted the copper rings on the projectile and added steel rings. I welded the last steel ring to the projectile.
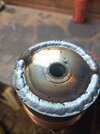
I turned everything to size, gave the new driving bands the right profile and added the groove to fit the case. A light coat of primer prevents rust while I wait for some time to restore the rest of the projo.
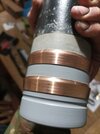
Now I have decided to try something new, something I've been thinking about for a long time: Making real bands, from real copper. It will involve a little bit of surgery for the projo, but it is worth a try. If pictures of projectile-surgery are going to upset you, you might want to turn away for a little while ;-)
This is the patient for today, a 17pr APCBC shell that I bought years ago. The previous owner tried to putty the bands and painted them in copper colour. Looking good from far, but far from good. Step 1 is to remove the putty and measure the width of the missing bands.
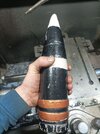
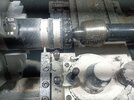
After this I machined the projectile to a smaller diameter.
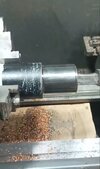
I made a ring from resin to make sand molds and melted scrap pieces of driving band that I saved from previous projects. I casted the molten copper in the sand molds and made two copper rings.
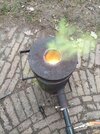
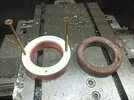
The inner diameter is turned to match the outer diameter of the projectile on the machined part.
I fitted the copper rings on the projectile and added steel rings. I welded the last steel ring to the projectile.
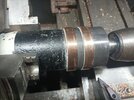
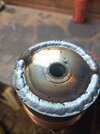
I turned everything to size, gave the new driving bands the right profile and added the groove to fit the case. A light coat of primer prevents rust while I wait for some time to restore the rest of the projo.
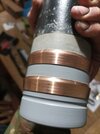