I'm often asked for No5 centre tubes by collectors & quite often they end up not fitting the grenade they were intended for . Usually this is due to the fact that they won't screw all the way in . The reason for this is the MASSIVE differences in casting tolerances . If you look at the pictures I've included , you can see the top of the det. tubes can be as much as 4mm lower on some compared with others & the slope of the end is much more pronounced . This means they foul the inside of the body before they screw all the way in . Some also have more threads than others . The difference on brass tubes is even more pronounced . I know some early grenades did n't have the internal recess at the top for the tube to fit into but I don't think that explains all the problems . I can only assume the tubes were made to fit the individual casting runs by the hundreds of different makers & were never meant to be interchangeable in the first place . This problem never occurs with No36's as all parts seem to be interchangeable irrespective of manufacturer .
I know Tom has been doing a lot of research on WW1 Mills & , perhaps , he could shine a light on the subject .
I hope this is of some interest to all those avid Mills collectors out there !
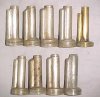
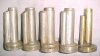
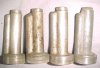
I know Tom has been doing a lot of research on WW1 Mills & , perhaps , he could shine a light on the subject .
I hope this is of some interest to all those avid Mills collectors out there !
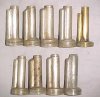
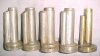
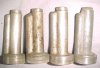